精益质量管理模型简述
环绕生产与质量主题,当前国内外已形成了多种理论和方法。最引人瞩目的当属ISO9000质量管理体系、精益生产管理(Lean Production)、六西格玛管理(Six Sigma)。ISO9000质量管理体系十多年来在国内承受企业热捧,证书需若是重要原因,但不可否认ISO9000质量管理体系本身的科学性和应用价值。精益生产管理与六西格玛管理近年来在国内承受追捧,精英企业理论实践一体的明星示范效应功居至伟,其理论方法的实用价值功不可没。
上面所提及的三种理论方法即使在我国应用过程中存在一部分不足和偏差,但各自均是值得深入研究和应用的管理模式。我们应目睹,这三种理论方法均是舶来品,是西方先进企业管理精华的提炼,尽管科学的理论方法不应有国界之分,但管理学科自身所具有的软性和弹性特质,使我们在借鉴应用这些理论方法时有必要结合国情。从我国企业广泛管理情况和管理方法需求出发,对相关理论方法执行创新探索应当是有必要的。
从生产系统综合改观的角度,精益生产管理、六西格玛管理理论方法可以有效结合,ISO9000质量管理体系相关思想也可借鉴其中。此种结合就是华安盛道研究倡导的精益质量管理模式(Lean Quality)。如下图所示:
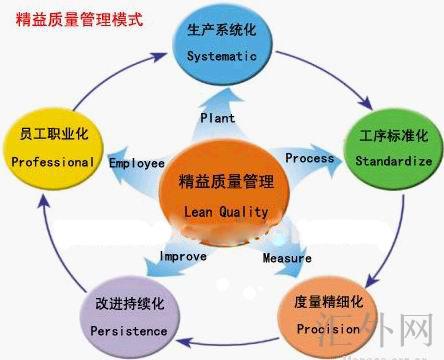
精益质量管理由五大子系统构成,分别为雇员职业化、生产系统化、工序标准化、度量精细化、改进连续化,这五方面是企业推行精益质量管理的五大法宝。这五大法宝各自又由有关要素构成,进而使精益质量管理形成体系。精益质量管理模式是环绕生产作业系统质量、效率、成本综合改观这个目标,吸收借鉴精益生产、六西格玛、ISO9000体系的优秀成果,并结合我国企业的事实情形而形成的。
精益质量管理模型五大法宝
1、雇员职业化
精益质量管理五大法宝之一是雇员职业化。精益质量管理将雇员职业化放在一个非常突出的位置,这是与精益生产、六西格玛、ISO9000体系的一个明显区别。精益质量管理借鉴相关管理革新项目成败经验教训,将雇员职业化作为推行精益质量管理革新的首要核心要素。
精益生产(LP)模式因为日本,差不多是丰田生产方式(Toyota Production System,TPS)的代名词,精益生产模式先天打上了日本企业文化的烙印,其体系架构是基于日本企业文化特质设定的。精益生产中5S提及了雇员素养,提及了多能工,这几方面还不充分,强度还不够。在工业化成熟的国家和地方,谈职业化如同我们当下还谈上班不要迟到,已属起码的职业举动,而我国雇员职业化与西方对比差距却很大,应当大力倡导和提高。很多西方理论方法在我国水土不服,这与我国企业整体职业化水平偏低不无关系,精益生产推行难度大固然有多种原因,把雇员职业化这道阻碍大力克服应是企业必选的重要措施。
六西格玛管理重视人的原因,创造了绿带、黑带、黑带主管等(GB、BB、MBB)资质体系,以促进企业人才的培养和六西格玛的推行。如同基础教育和高等教育的区别一样,雇员职业化如同我国广大企业在执行基础教育,而绿带、黑带等则象已完成基础教育的企业在执行高等教育。对我国大量企业来说,谈雇员职业化以及提高雇员职业化水平则更具广泛实用意义。
ISO9000质量体系“6.2人力资源”中提出“基于适当的教育、培训、技能和经验,从事影响产品质量工作的人士应是能够胜任的。”其着眼点许多的倾向于质量有关人士,其有关人的要求的高度不够,系统性也不够。
精益质量管理中雇员职业化从企业与雇员两个方面提出要求,为求全面促进雇员职业化水平的提高。雇员职业化企业角度构成要素包含:文化理念、任职资格、组织管理、激励机制、考评机制、职业发展。雇员职业化雇员角度构成要素包含:职业资质、职业意识、职业心态、职业道德、职业举动、职业技能。企业要素是促进雇员职业化的外围条件,包含人力资源管理的一部分着重工作。雇员要素是促进职业化的本身条件,首要靠本身的修炼和提升,外围企业要素对其有重要影响。
对生产作业系统来说,雇员职业化包含员工的职业化,也包含主管以及更高层次人士的职业化。虽因角色不足,但都对作业系统质量、效率、成本造成影响。雇员职业化是精益质量管理的首要核心成功要素,是精益质量管理的一大法宝。
2、生产系统化
生产系统化是推行精益质量管理的第二大法宝,是精益质量管理的核心子系统,其研究对象是生产作业系统,系统化的涵义就若是从作业系统全局谋求影响质量、效率、成本的全局性核心原因,采取系统化的方法谋求困难的根本处理,以高达作业系统质量、效率、成本的综合改观。
精益质量管理生产系统化首要借鉴了精益生产的首要工具和方法,但有所不足。生产系统化着重工具包含:JIT/MRP、生产布局、自动化、标准化、5S、目视/看板等。其中JIT/MRP是涉及生产系统全局的软性核心要素,生产布局是涉及生产系统全局的硬性核心要素,均对生产效率有着全局性影响。自働化、标准化对质量和效率均有重要影响,其中标准化则涉及更普遍,重要性相对更突出,是精益质量管理的第三大法宝。5S、目视、看板等均是保证生产系统作业效率的重要工具。
MRP即物料需求计划,因为美国,其与JIT思想不同,JIT强调后工序物料需求的拉动和传导,而MRP则是企业中央计划指令系统,其通过运用MRPII(制造资源计划)或ERP(企业资源计划)软件系统计算各工序的应投料量。
尽管JIT与MRP逻辑差别很大,但均为科学方法,企业推行精益生产时不应固守JIT、看板等丰田公司采取的方式,应灵活运用。MRP是生产系统化的重要工具,其能适应频繁转产以及产品结构复杂多样化的情形,并具计算快速全面和网络化优势,其较JIT、看板更具实用性。推行精益生产或生产系统化,JIT可作为一种子理念和追求目标,从事实操作中借助更先进的工具如MRP应该更有出路。
精益质量管理倡导的生产系统化以精益生产思想和工具为主体, 并放开引入MRP作为达到精益管理的重要工具,目标均是为谋求作业系统质量、效率、成本的综合改观,而非局限于丰田生产方式所用工具。
3、工序标准化
工序标准化是推行精益质量管理的第三大法宝,工序标准化也是生产系统化的重要构成部分。将工序标准化列为精益质量管理的第三大法宝,是基于工序在生产过程的重要地位。工序是产品形成过程的基本单位,工序质量直接决定着产品的质量和生产效率。工序质量受多方面原因影响,概括起来首要有六个方面,即5M1E(人、机、料、法、环、测),组成工序标准化的六大要素。
工序质量受5M1E原因的影响,5M1E原因又受外围有关工作质量的影响。工序标准化要求5M1E要素标准化,也隐含着对5M1E外围有关工作标准化的要求。工序标准化就是要通过5M1E要素的标准化保障工序质量和效率。
工序质量的重要评价指标是工序能力指数,工序质量直观结果显现为合格率、单位工时等指标。工序质量也可通过直方图、控制图执行评价和分析。工序质量受5M1E等外部原因的影响也能反应外部原因的改变,工序质量的易评价性就可促进对5M1E及外围工作的有效评价和改观。
工序标准化是精益生产、六西格玛、ISO9000体系共同的管理要求,是生产管理、质量管理、成本管理等职能管理共同的要求。原有职能管理模式产生工序标准化的多头管理,各类要求相互间有交叉重叠也有遗漏,工序标准化仍未深入细致和协调统一,工序标准化应综合体现质量、数量、成本等的标准化要求。
精益质量管理目标是谋求作业系统质量、效率、成本的综合改观,对作业系统不刻意区分生产职能和质量职能,从项目角度也不区分为精益生产项目或六西格玛项目,并倡导多种工具方法的综合运用。精益质量管理将工序标准化作为第三大法宝,就若是促进企业愈加重视工序标准化,并打破职能界线联合促进工序标准化,构筑起作业系统质量、效率、成本综合改观的坚实基础。
4、度量精细化
度量精细化是精益质量管理的第四大法宝。度量是六西格玛管理和ISO9000质量体系特别强调的管理要求,在生产管理中常以统计一词表达有关生产结果。度量与统计是有区别的,度量隐含着与标准的比照,报告结果是处在坐标系中的。而统计则未强调与标准的比照,对偏差常不作深究。
精益质量管理综合精益生产管理与六西格玛管理各自所优点,充分认识到度量对工作改观的重要意义,将度量精细化作为精益质量管理的第四大法宝。度量精细化首要包含六类指标:西格玛水平(Z)、工序能力指数( Cpk)、 合格率(FTY、RTY)、不良质量成本(COPQ)、价值识别度量、浪费识别度量。
精益生产提出了价值原则,提出了生产中的七项浪费。六西格玛管理提出了不良质量成本(COPQ)。环绕价值、成本和浪费,精益生产与六西格玛均力图达到改观。精益质量管理综合研究生产作业系统,将谋求作业系统质量、效率、成本综合改观作为目标。精益质量管理针对作业系统就可达到博采众长,取长补短。
借鉴六西格玛管理对度量重要意义的认识:我们不重视不度量的,我们对不度量的无所作为。精益质量管理将度量的规模从质量领域气扩大化,延伸至生产、价值、浪费、成本等领域。JIT准时制被列为精益生产管理的两大支柱之一,JIT即要求上下游工序间达到交付“精准的产品、精准的数量、精准的时间”。JIT在精益生产管理中并没有有效度量,而借助西格玛管理方法,JIT三要求可纳入度量,如评价交付时间的西格玛水平。
度量精细化就是要将有必要度量的对象尽或许的纳入度量评价体系中,通过分量比较发现困难和不足,通过分量树立标杆或目标,通过分量促进改观。
5、改进连续化
改进连续化是精益质量管理第五大法宝。连续改进是精益生产、六西格玛、ISO9000体系共同强调的理念。改进连续化在精益质量管理中起承前启后作用,是度量精细化的保持和要求,缺少改进连续化则度量的作用将缩减,而雇员职业化、生产系统化、工序标准化则会缺少新的动力和要求,管理将止步不前甚至于倒退。
精益质量管理强调改进连续化,除理念倡导外还包含具体的组成要素和保障条件。改进连续化首要包含如下六类要素:市场意识、领导作用、全员参与、工具方法、测量评价、奖惩措施。这六类措施是改进连续化的保障条件。
市场意识影响改进连续性的活力强弱,影响改进标杆的高与低;领导作用影响改进连续性的组织强度和资源配置;全员参与赋予改进连续性以民众基础和团队力量;工具方法是改进连续性的方法体系,5W1H、PDCA、QC小组、改进小组、六西格玛项目等均是促进改进连续性的工具方法;测量评价是将改进连续性纳入测量和管理中,让改进连续性因测量和评价而焕发生机和动力;奖惩措施将改进连续性纳入管理和激励体系中,是测量评价的保持和要求,促进改进真正达到连续性。
改进连续性及组成要素首要借鉴了ISO9000八项质量管理原则,如以顾客为关注焦点、领导作用、全员参与、连续改进。改进连续性借鉴ISO9000理论精华,并借鉴精益生产、六格玛等理论方法中度量、改观、激励等理念方法,能促进改进连续性真正落到实处,收到实效。
精益质量管理模型的特点
环绕精益质量管理模式的基本思想:“质量基准、杜绝浪费”,其特点可以凝聚为四点: “贴近客户, 善待雇员,低成本,零缺陷”,见下图:
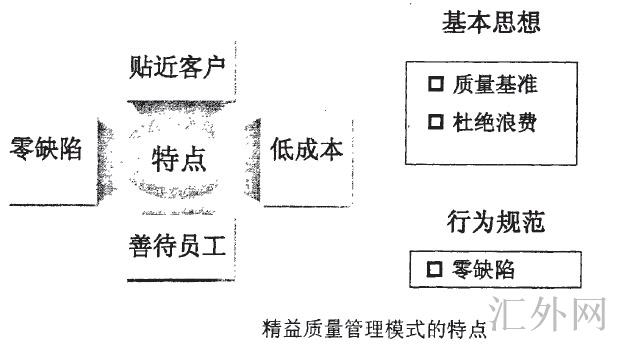
精益质量管理模型的方法
为了达到制造产品所应有的模式,首先要设定标准,其次是连续提升标准的质量。为了提升标准的质量,PDCA(plan-do-check—action)管理系统的良性循环比什么都重要。
在引入精益质量管理方法的时机,将“工作标准化”及“PDCA循环”作为开展各类工作的基本管理方法来学习,以保证工作效率平稳地提升。
精益质量管理模型与有关理论方法的比较
1、精益质量管理与精益生产管理的比较
根据丰田生产模式研究成果,精益生产模式的首要框架下图所示。标准化、平顺化、改观作为精益生产模式的基础;准时制、自働化作为精益生产模式的两大支柱;5S、目视管理、看板管理、迅速换模、全面生产维护(TPM)等是精益生产重要工具;精益生产追求的目标是卓越经营,包含最佳的质量、成本和交货期等。
精益生产模式首要工具被纳入精益质量管理生产系统化模块当中,部分理念体现于工序标准化、改进连续化中。

2、精益质量管理模型与六西格玛管理的比较
参照三星六西格玛运营革新模式,六西格玛管理模型可概括为下图形式。六格玛通过四个子系统达到过程经营能力的提升,分别是合适的人士、恰当的项目、正确的方法、精准的度量。合适的人士首要由黑带主管、黑带、绿带构成,通过项目团队促进人才培养和业绩提高。恰当的项目,首要通过VOC客户声音、CTQ核心质量要求等确定,并达到要求。正确的方法首要包含DMAIC、DFSS(六西格玛设计)等,通过DMAIC达到效率提升,通过DFSS达到价值的创造。应用6SIGMA方法达到业绩目标,有三种载体,分别为6 SIGMA过程(PFSS)、6 SIGMA策划(DFSS)和6 SIGMA组织(OFSS)。精准的度量首要包含COPQ不良质量成本、西格玛水平,以反应过程能力和成本损失等。
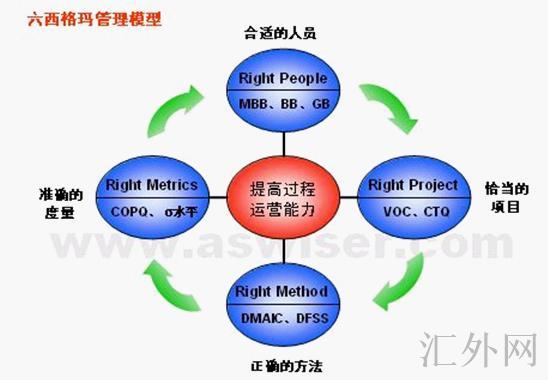
DMAIC分别代表定义、测量、分析、改观、控制。比较发现,精益质量管理对六西格玛有较多借鉴,如有关人士、度量、改观。精益质量管理在借鉴六西格玛思想方法基础上,加入了精益生产管理的优秀成果,形成了综合改观生产与质量等方面的模式。
3、精益质量管理与ISO9000质量管理体系的比较
ISO9000:2000标准提出了以过程为基础的质量管理体系模式。以顾客要求作为总的输入,以产品输出保证顾客满意。通过管理职责、资源管理、产品达到、测量分析与改进循环达到质量管理体系的连续改进。
ISO9000质量体系提出了八项质量管理原则,如下图所示。八项质量管理原则分别是:以顾客为关注焦点、领导作用、全员参与、过程方法、管理的系统方法、连续改进、基于事实的决策、与供方互利关系。

精益质量管理借鉴了ISO9000质量管理体系的核心思想和原则,并结合精益生产管理、六西格玛管理执行了组合创新,以使精益质量管理具有较强的科学性和实用性。
概括来说,精益质量管理以作业系统质量、效率、成本综合改观为目标,综合借鉴和吸收精益生产管理、六西格玛管理以及ISO9000质量体系等的理念和方法精华,综合形成的由雇员职业化、生产系统化、工序标准化、度量精细化、改进连续化五大子系统组成的管理框架。精益质量管理模式还属于摸索完善阶段,仍需要持续优化改进,也仍需要在应用中执行检验和锤练。